- Water treatment
- Blending system
- Bottle blowing system
- Bottled water filling line
- Bucket water filling line
- Packing system
- Juice/tea beverage production line
- Carbonated beverage production line
The principle of filling machine you know?
1) Normal pressure method
Normal
pressure method, also known as pure gravity method, that is, under
normal pressure, the liquid material to rely on self-weight flow into
the packaging container.Most of the free flow of gas-free material can be filled with this
method, such as liquor, wine, milk, soy sauce, vinegar and so on.
(2) isobaric method
Equal
pressure method, also known as pressure gravity filling method, that
is, higher than atmospheric pressure conditions, the first charge of the
packaging container, so that the formation of the tank with the same
pressure, and then rely on the infusion of pouring material into the
weightInside the packaging container.This method is generally used for gas-containing beverages such as beer, soft drinks, sparkling wine and other filling.The filling of this method can reduce the loss of CO2 contained in
such products and prevent excessive foaming during filling and affect
product quality and quantitative accuracy.
(3) Vacuum method
Vacuum method is carried out under the conditions of less than atmospheric pressure, can be carried out in two ways:
(A) Differential pressure vacuum type
That is, the tank is at atmospheric pressure, only the packaging
container to make a vacuum, liquid material to rely on the tank and the
pressure difference between the container to produce flow to complete
the filling, domestic this method is more commonly used.
(B) gravity vacuum type
That
is, the tank is in a vacuum, the packaging container is first pumped to
form a vacuum equal to that in the tank, and then the liquid material
flows into the packaging container by its own weight, because the
structure is more complicated and less domestic.Vacuum
filling a wide range of applications, it is suitable for filling a
slightly larger viscosity of liquid materials, such as oil, syrup and so
on.Also
suitable for filling vitamins containing liquid materials, such as
vegetable juice, fruit juice, etc., the bottle to form a vacuum means
that the liquid material to reduce the contact with the air to extend
the shelf life of the product, vacuum method is also suitable for
filling toxicMaterials such as pesticides, etc., to reduce the spill of toxic gases, improve working conditions.
(4) pressure method
The
use of mechanical pressure or pressure, the irrigation material will be
squeezed into the packaging container, this method is mainly used for
filling thick viscous materials, such as filling tomato sauce, meat
emulsion, toothpaste, balsam and so on.And
sometimes can be used for soft drinks a soft drink filling, then rely
on the pressure of the water itself directly into the bottle without
inflatable pressure, which increased the filling speed, the formation of
the bubble because of the colloid is still easy to disappear,On the filling quality have a certain impact.
In this paper, the filling method of filling machine is determined:
For
the general consumption of liquid materials such as bottled milk,
bottled alcohol, carbonated drinks, etc., can be used to fill the
pressure method, vacuum filling method, but taking into account the cost
of isobaric filling method can effectively reduce the loss of CO2,To
maintain the quality of gas-containing drinks, and to prevent excessive
filling in the bubble, to ensure accurate filling measurement.Therefore, this paper uses isobaric filling method.
The
bottle in the filling machine in turn: 1, into the air, 2, into the
liquid back to the gas; 3, stop the liquid; 4, remove the remaining
liquid 4 steps.At the same time the production line of a variety of detection status
sensors all access to the PLC, the PLC according to the sensor detection
status through the preparation of a good program to control the entire
system work.
Filling valve components from the liquid valve, gas pipe, valve, centering cover, exhaust valve and other components
PLC acquisition signal:
1. Filling machine bottle tray pressure
2. Centering pressure
Air pressure
4. defective picker pressure
5. Maximum hydraulic pressure
6. Minimum hydraulic pressure
PLC output signal:
Conveyor belt
2. bottle tray
3. Valve
4. Filling the valve
5. defective lights
6. defective conveyor belt
7. defective picker
8. Feeding valve
9. return air tube
10. Gripping machine
11. Packaging machine
Normal workflow
Press the start button to transfer the wheel and the filling machine to start.Then press the conveyor start button, filling machine into the bottle conveyor belt start.After
the bottle enters the conveyor belt, the bottles are equally spaced
into the bottle tray lifting mechanism by passing the wheels.When
the tray detects the pressure, the pallet piston gives the pallet lift a
pressure, and the tray begins to take the bottle up.In
the time of the rise of the tray, the maximum rise time is 6S. If the
pressure is detected, the tray will stop rising and then the valve will
open to start filling the bottle.The maximum inflation time is 6S.When the valve to detect the pressure, then stop charging CO2, the liquid valve open, start filling.Filling time is 6S.After
filling, the tray begins to drop, the process of lowering the liquid
valve at the same time, the return air pipe work, open the exhaust and
remove the liquid operation.The
finished bottle is then passed through a certain angle and is sent by
the delivery wheel, and the bottle tray continues to move forward into
the next cycle.
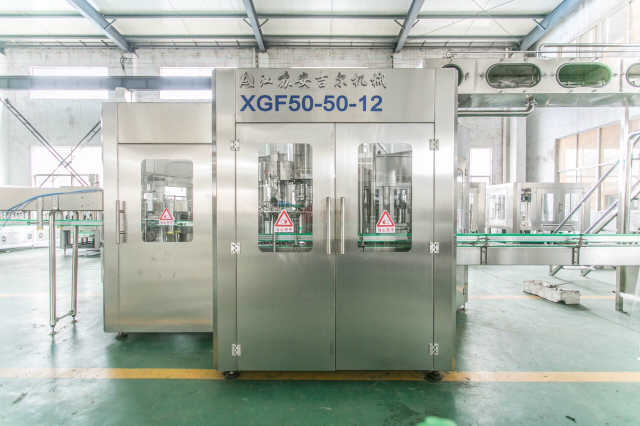
When a defective is detected:
1. When the defective bottle is used
When
the maximum filling time is increased by 6S, the pressure is not
detected when the maximum level of the tray is increased (the bottle is a
burst bottle, the height is insufficient), the tray starts to drop, and
the defective light is on and the tray is lowered 6S. Decrease the tray to wait for the next cycle. At the same time defective detector start.
2. When the defective bottle is broken:
Then
the normal filling process, when the maximum inflatable time 6S to the
time, the valve did not detect the pressure (broken bottle, CO2 filled
dissatisfaction), then stop charging CO2, while the bottle tray began to
decline, defective lights, tray down time 6S , The drop down the tray waiting to enter the next cycle, while defective detector start.